Elektor Seminar Hanau 05.06.2013
zurück zum Hauptartikel Elektor Seminar
Elektor-Seminar: Rapid SMD-Prototyping mit TARGET 3001! und PCB-POOL®
Prototypen aus dem Pizza-Ofen
Bing - Platine fertig! So klang es am 05.06.2013 im Arcadia Hotel in Hanau beim Elektor Hands On Seminar zum Thema:
"SMD Löten selbst gemacht"
Ja, es geht. Man kann einen selbst entwickelten Leiterplatten Prototypen mit SMD Bauteilen eigenhändig bestücken und in einem handelsüblichen Back-Grill-Ofen Reflow-löten. Dies erfuhren 21 Teilnehmer in einem 7-stündigen Elektor Seminar am Beispiel eines kleinen Schaltungsprojekts (digitaler Brettspiele-Würfel). Gemeinsam wurden Schaltplan, Leiterplatten- und Frontplattenlayout mit TARGET 3001! entwickelt und zur Produktion in Auftrag gegeben. Jeder Teilnehmer bestückte seine bereits im Vorfeld produzierten Leiterplatten komplett mit SMD Bauteilen und konnte das Verlöten der Bauteile auf seinem Board im Reflow-Ofen beobachten. Dann verschraubte er seine bestückte Leiterplatte mit der Frontplatte und dem Batteriehalter. Am Ende des Tages lag ein professionell gestalteter, digitaler Spielewürfel auf dem Tisch, der auf Tastendruck zufällig jeweils die Augen 1 bis 6 anzeigt.
Möglich macht dies die perfekt integrierte Prozesskette zwischen dem Leiterplattenhersteller Beta Layout GmbH und der Leiterplatten Layout CAD Software TARGET 3001!. Neben der Leiterplattenproduktion gehören auch Frontplattenproduktion 3D-Druck und die neuartige RFID Technologie für Leiterplatten ins Portfolio der Beta Layout GmbH.
Ein weiterer Seminartag fand am 11.09.2013 in München statt.
Im ersten Teil erläutert Harald Friedrich die Produktidee und den Schaltungsaufbau. Es folgt das Hereinholen einiger Bauteile in den Schaltplan über die Bauteildatenbank sowie die Signalverlegung zwischen den Bauteilen im Schaltplan
Im nächsten Schritt werden die Gehäuse im Layout platziert und die Leiterbahnen angeschlossen. Mit dem Autorouter ist dies schnell erledigt. Im weiteren Verlauf erläuterte Herr Friedrich die Simulation sowie die 3D-Ansicht und ihre Bedeutung für die Weiterverarbeitung der Platine in mechanischen CAD Systemen. Über das STEP/STL Format kann ein Kunststoffdummy der bestückten Platine erzeugt werden.
Schaltplanerstellung, Platinenenlayout, Simulation und Frontplattendesign ist einiges an Inhalt. Hier heißt es: Alle Antennen auf Empfang. Da das Projekt in verschiedenen Stadien der Entwicklung verfügbar ist, können alle Teilnehmer immer wieder an einem gemeinsamen Punkt weiter machen.
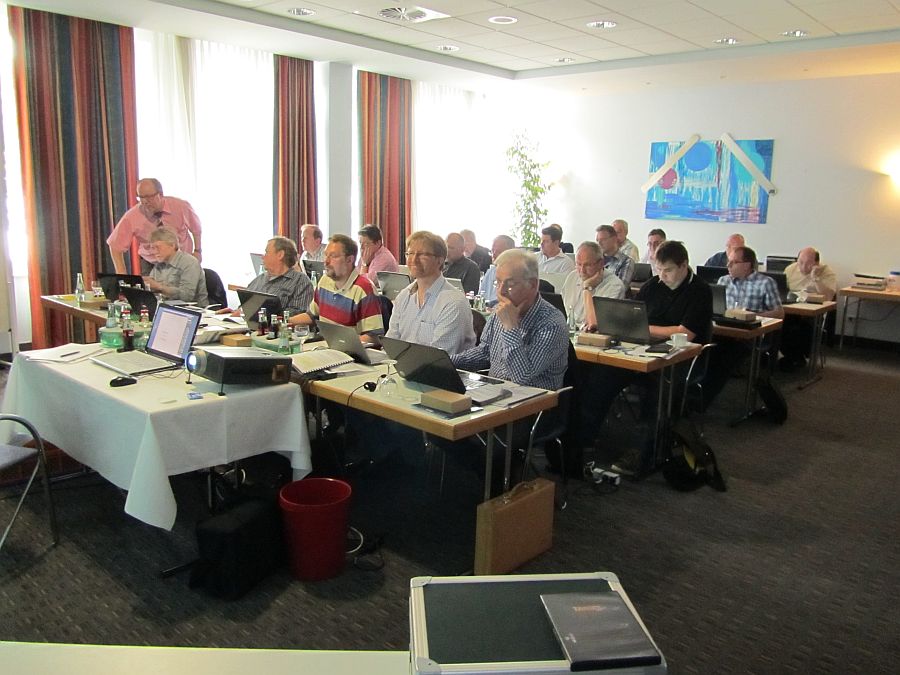
Ausreichend Zeit blieb dennoch zum Fragen Beantworten und am Rechner zu schauen, wenn es irgendwo hakte.
Links ein im Vorfeld mit dem Lötkolben von Hand bestücktes board. Bauteile schief, Lötstellen klumpig, schwierig zu kontrollieren, schwierig zu reparieren (ein früher Designfehler musste mit einer Drahtbrücke behoben werden). Links das selbe Layout handbestückt aber Reflow gelötet. Diese Qualität zu erreichen, war das Ziel des Seminars.
Gernot Seeger (Beta Layout GmbH) erläutert das Leistungsspektrum der Beta Layout GmbH. Leiterplattenproduktion, Integration der RFID Technologie in die Leiterplatte, 3D-Druck (Laser-Sinterverfahren), Bestückung von Prototypen ab 1 Stück, Frontplattenproduktion mit Digitalbedruckung
Ein Mitarbeiter von Beta Layout erklärt die Anwendung einer Lotpastenschablone. Sie besteht aus dünnem Edelstahl und hat Aussparungen da, wo sich die Lötpads befinden. Jetzt wird sie passgenau auf die Platine gelegt. Mit einen Rakel wird Lotpaste über die Schablone gezogen. Wie im Tiefdruckverfahren bleibt Paste in den Löchern hängen und bedeckt so die Lötpads.
Der Applikationsrahmen ist magnetisch. Dies erlaubt eine unverrutschbare Einbringung der Platine. Mit Hilfe einer Passermarke wird die Schablone exakt darüber ausgerichtet und mit Magneten am oberen Rand befestigt.
Jetzt wird die Lotpaste aufgerührt. Lotpaste sollte kühl gelagert werden, denn sie hat ein Verfalldatum.
Der Applikationsrahmen hat an der oberen Kante ein Scharnier, so dass die Pastenschablone einfach weggeklappt werden kann um die Platine wieder zu entnehmen. Das hat den Vorteil, dass eine folgende Platine nicht neu ausgerichtet werden muss. Man legt sie wie bei einem Kopierer in die Ecke oben rechts und klappt die Schablone wieder ab. Ein mit Leiterplattenstreifen von Hand gefertigter Rahmen auf einem Sperrholzbrett mit Klebeband fixiert, tut es ebenfalls. Wenn man die Pastenschablone nur am oberen Rand mit Klebeband festklebt, hat man den gleichen Scharniereffekt wie beim Magnetrahmen. Siehe oberer Rand des Bildes.
Jetzt wird die Lotpaste über die Schablone gerakelt. Der Rakel ist ein baumarktüblicher Japanspachtel.
Hier sieht man die hochgeklappte Schablone nachdem die Lotpaste aufgerakelt wurde. Jetzt kann die Platine entnommen werden und die SMD-Bauteile mit der Pinzette in die Paste gedrückt werden. Die Lotpaste hat etwa die Konststenz von Abschmierfett, die Bauteile haben Reiskornformat. Die Adhäsionskräfte der Lotpaste halten die Bauteile fest.
Der mangnetische Schablonenapparat. Der weiße Streifen ist flexibler Magnetstreifen. Er hilft beim Festhalten der Platine. Der obere Rand ist zurückgeklappt, die Schablone hängt daran. Eine neue, lotfreie Platine kann eingelegt werden.
Das ist eine SMD Leuchtdiode. Sie hat etwa die Abmessung 2mm x 1mm. Die Anode ist bei den beiden grünen Punkten.
Mehrere Leuchtdioden. Unten ist da, wo der grüne Strich ist. Die Anode ist da, wo die beiden grünen Punkte sind. Die Lupe bitte!
... wirds schwierig. Oft ist das Öffnen der Verpackungen schon eine Herausforderung. Fällt ein Bauteil auf den Teppich, ist es weg.
Mit viel Licht und Lupe geht's. Durch den präzisen Lotpastenauftrag sind nur geringe Positionskorrekturen möglich.
Die Platine ist fertig. Jetzt muss nur noch der Draht für die Spannungsversorgung angelötet werden und dann heißt die große Frage: "Würfelt's?" Die Platine im Hintergrund ist eine Referenzplatine. Ihre "Mächtigkeit" dient dem Steuergerät zur korrekten Temperatursteuerung.
Der Anschlussclip für die Spannungsversorgung ist angelötet. Eine professionelle Leiterplatte incl. Bestückung ist entstanden.
Die 3D Ausgabe in TARGET 3001! ermöglicht den Ausdruck der Leiterplatte in 3D. So entsteht ein Kunststoffdummy zur Prüfung der Passgenauigkeit respektive eventueller Kollisionen beim Einbau. Ein solcher Dummy entsteht im Laser-Sinterverfahren und ist im Vorfeld der Leiterplattenproduktion/Bestückung kostengünstig zu haben.
Die Frontplatte wurde in TARGET 3001! "über der Leiterplatte" konstruiert. Die Fräsbilder für die Bohrungen konnten deckungsgleich über den LEDs bzw. dem Taster abgesetzt werden. Die Frontplatte passt exakt auf die Leiterplatte.
Von hinten wurden Gewindebolzen in die Frontplatte eingepresst - von vorne nicht zu sehen. Sie dienen der Befestigung der Leiterplatte und der Batteriehalterung.
Die Batteriehalterung. Sie wurde mit einem mechanischen CAD System designt und mit dem 3D-Drucker kostengünstig ausgedruckt. Dieses Objekt war nicht Gegenstand des Seminars. Es wurde von den PCB-POOL-Spezialisten beigesteuert. Die Löcher passen genau auf die Gewindebolzen der Frontplatte.
Aufbau des Endprodukts. Grün - die Leiterplatte mit LEDs und den anderen Bauteilen. Alu - die Frontplatte. Weiß - die 9V Batteriehalterung. Die Gewindebolzen sind von hinten in die Frontplatte eingepresst, so dass deren Front keine Montageelemente zeigt. Die Lichtleiter aus Plexiglas werden frontseitig durch die Aluminiumplatte eingesteckt, so dass sie exakt auf den LEDs sitzen. Alle drei Elemente werden gemeinsam "von hinten" verschraubt.
Die Lichtleiter aus Plexiglas werden frontseitig durch die Aluminiumplatte eingesteckt. Sie haben an einem Ende eine Wölbung mit einem Kragen so dass sie nicht durchrutschen. Die vier winzigen Stege unter der Wölbung werden beim Eindrücken verformt und sorgen so für Halt im Bohrloch.
Ein Mitarbeiter von Beta Layout (links) demonstriert einem Teilnehmer die Funktionsweise des eingebauten RFID Chips. Über das Lesegerät gehalten, offenbart die Platine ihre individuell programmierten Daten: Welches Projekt, welche Revisionsnummer, welche Bestückungsvariante oder was immer programmiert wurde.
Zufriedene Gesichter am Ende eines gelungenen Seminartages. Harald Friedrich (rechts) mit einem Teilnehmer. Wir freuen uns schon auf München.
zurück zum Hauptartikel Elektor Seminar